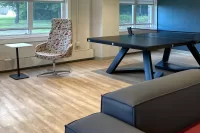
Campus Construction Update: Sept. 25, 2015
As the Maine Masonry bricklayers finished their work on the north side of the student residence being built at 65 Campus Ave., the before-and-after difference was striking in a surprising way.
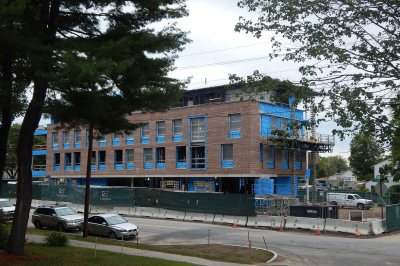
65 Campus Ave. is looking eminently bricky on an overcast Sept. 10, 2015. Notice the new sidewalk “bumpout” at bottom. (Doug Hubley/Bates College)
Uniform brickwork has replaced the bold blue weatherproof film on the walls, and windows that were once gaping black openings are now blanked with translucent polyethylene sheeting. But what’s really weird is that, although we know the bricks have actually made the building slightly bigger, we could swear it looks smaller.
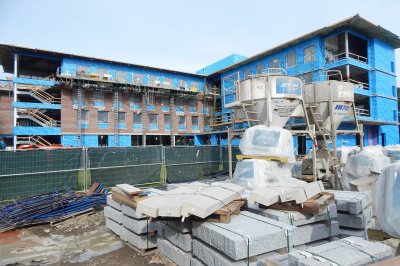
With the new student residence at 65 Campus Ave. in the background on Sept. 21, 2015, granite and pre-cast concrete forms await their turn with the masons. The conical bins hold mortar. (Doug Hubley/Bates College)
Yet another reminder, as if we needed it, that perception isn’t reality. “The brick chosen for the buildings is both matte and dark, so it is a light-absorbing surface rather than light-reflecting,” explains Pamela Johnson, associate professor of art and visual culture. “So now the walls appear to recede.
“The small-scale patterning in the brickwork also adds to the illusion of receding space,” she adds.
“But most important, perception of color is contextual. The brick integrates the new dorms with the buildings across the street, so the new construction merges with old into one harmonious view.”
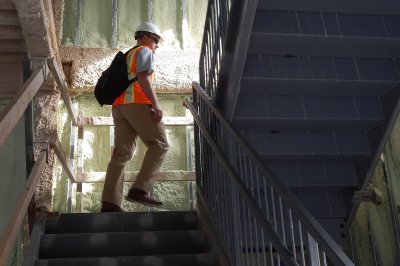
Chris Streifel, Facility Services project manager for the Campus Avenue dorm construction, climbs stairs at No. 65 on Sept. 21, 2015. (Doug Hubley/Bates College)
With that in mind, we can expect No. 65 to continue its apparent shrinking act through the coming weeks, as the masons have essentially finished with the second of the six major walls (a narrow west-facing side) and are going great guns on the long south wall.
The other residence constituting this phase of the Campus Life Project, No. 65’s younger sibling at 55 Campus, is playing the receding trick as well, as Maine Masonry started bricking up its west wall during Labor Day week and rounded the corner to the wall nearest Campus Avenue this week.
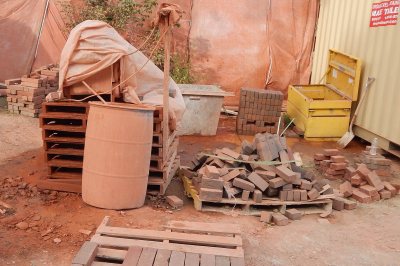
Seeing red: Surrounded by brick dust, a masonry saw on the 65 Campus Ave. work site is covered up for the night. (Doug Hubley/Bates College)
Early evidence that the masons are on the scene includes the appearance of Hydro Mobile “mast climbing work platforms” — impressive mechanized scaffolds that use hydraulic motors to lift the masons and their weighty materials to the desired height. In the manner of a cog railway, the motors raise or lower the platforms by turning gears that engage a toothed rack on the masts that support the whole contraption.
Those motors will do some heavy lifting in the coming months. By the time their work is complete, Maine Masonry workers will have placed 138,000 bricks, weighing in at 552,000 pounds (all figures are approximate); 7,500 square feet of split-face granite veneer, or 1,237,500 pounds; and 1,950 linear feet of precast concrete trim, or 191,500 pounds.
(Thanks to Tim Schneider, who is running the Bates residence job for Consigli Construction, for those figures.)
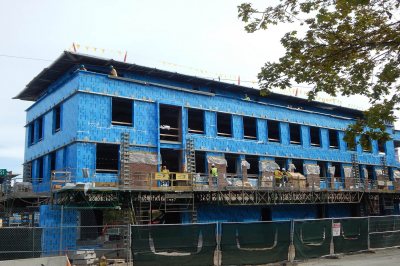
Bricklayers on the Hydro Mobile mast-climbing platform on the Bardwell Street side of 55 Campus Ave. on Sept. 21, 2015. (Doug Hubley/Bates College)
Meanwhile, the residence facades are about to evolve again as Oakes & Parkhurst Glass of Augusta starts installing window units, possibly by the end of September. It’s a job that can’t be done until the bricklaying is done in a given area, so again the work will begin on the completely bricky wall of No. 65 that faces Campus Avenue, says Bates project manager Chris Streifel.
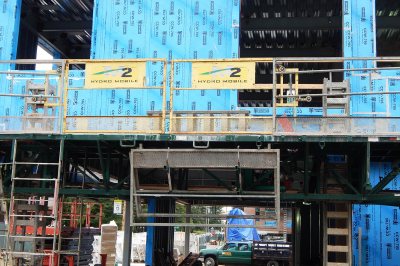
A Hydro Mobile self-elevating platform at 55 Campus Ave. on Sept. 10. Visible at right is the open-work mast that the platform climbs. (Doug Hubley/Bates College)
Mounted on wooden frames, the heavy poly sheets now sealing the windows at 65 Campus will be saved for re-use at No. 55 as the permanent windows replace them. O&P Glass, as it likes to be known, will also install the “storefront” glass — large glass sheets, not encased window units — that will allow dramatic views from the staircases and corners of the dorms.
With winter coming (as Campus Construction Update likes to say, repeatedly, to people who are new to the North), the building team is acutely aware that the more windows that are installed, the more weathertight the residences will be.
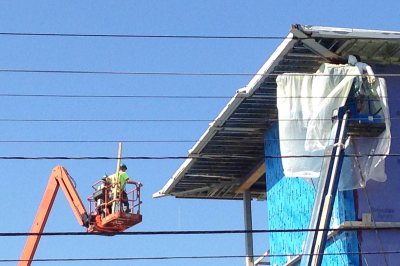
Technicians on two lifts working on the roof of No. 65 Campus Ave. on Sept. 16, 2015. (Doug Hubley/Bates College)
But the roofs have been waterproof for weeks now, thanks to a weather-barrier membrane covering them. The next step for roofers from the Lewiston division of Industrial Roofing Companies, Streifel notes, is to mount a wooden rim around the roof edges. This will provide a substrate suitable for attaching other roofing components.
“The roof membrane wraps over that and ties back in with the blue wall covering below,” Streifel explains, “so it’s wrapped 100 percent all the way around” to form a solid weather barrier.
Among the workers appreciating the increasingly weather-free interior of No. 65 are the wallboard hangers of Timberland Drywall of Gorham. They know better than most that it’s a problem when drywall becomes wetwall. “Unlike the wallboard on the outside of the building, the sheet rock on the inside is not treated against water,” says Streifel.
On the scene for most of September, Timberland has put metal wall studs in place through much of No. 65. A quick tour revealed striking expanses of shiny studs and dull gray doorframes, some set in place, some in big stacks awaiting installation.
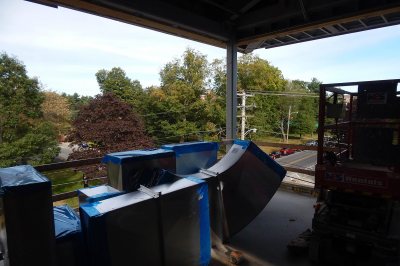
Ducts in a row: Seen past a stockpile of air ducts on the fourth floor of 65 Campus Ave., the trees at Central and Campus avenues are just starting to turn on Sept. 21, 2015. (Doug Hubley/Bates College)
One newly framed-in student room on the third floor is serving as a mockup or demonstrator where construction processes will be tried out before they are broadly applied — a tactic being employed in different areas in both buildings, and best exemplified by the freestanding wall mockup near the fence on the 55 Campus site.
In the case of the mockup bedroom, a single, “the idea is that we will finish that room far enough ahead of the others that we can learn from the intricacies of it,” Streifel says. “So we’ll see if the fan coil unit fits where it’s supposed to, outlets end up where they’re supposed to, and that everyone’s happy with the way that everything else is installed.”
“So if there’s something to learn there before we go on and repeat an operation 167 times” — the number of bedrooms in the two buildings — “we have the opportunity to make some changes.”
Streifel explains that the subcontractor for a given process will assign someone to do the mockup who will then serve as the resident expert when the wholesale execution of that process begins. “It’s a learning experience for that person, so they’ll understand what the expectations are for the work.
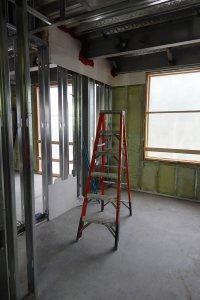
Watch this space: Serving as a mockup, this third-floor single bedroom at 65 Campus Ave. will be finished early in order to pre-test construction techniques. (Doug Hubley/Bates College)
“The contractor ends up with someone who knows exactly what to do, and they should be that much faster and have that much less corrective work to be taken care of later on.”
Timberland workers are also putting in the wallboard itself. “Typically they’ll do the tops of the walls first,” Streifel says, “because it’s usually the more challenging portion of it. There’s a lot of cutting, fitting, and sealing around pipes and beams and conduits.”
He adds that it’s typical to sheetrock one side of a wall at a time and then move on, leaving the other side open for utility installations and the code inspections that those installations require. Once those are done, the other side of the wall will be installed. That way everybody can keep working.
Can we talk? Campus Construction Update welcomes queries and comments about current, past, future, and imaginary construction at Bates. Write to dhubley@bates.edu, putting “Campus Construction” or “The ’60s! Now those were some hard winters!” in the subject line. Or use the comments system below.