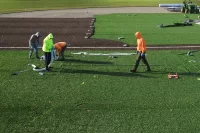
If every week brought the kind of excitement sparked up in late November by the hoisting of a large air-handling machine into Dana Hall’s attic, Campus Construction Update would be incapacitated by nervous exhaustion.
But these days, fortunately, the Dana renovation is about steady, soothing overall progress and not show-stopping crane choreography.
If we want to get all numerical about that progress, Bates construction administrator Jacob Kendall estimates that on a typical work day, there are 50 or 60 workers on site representing 10 trades. “There will be a body in every corner” getting something done, he says.
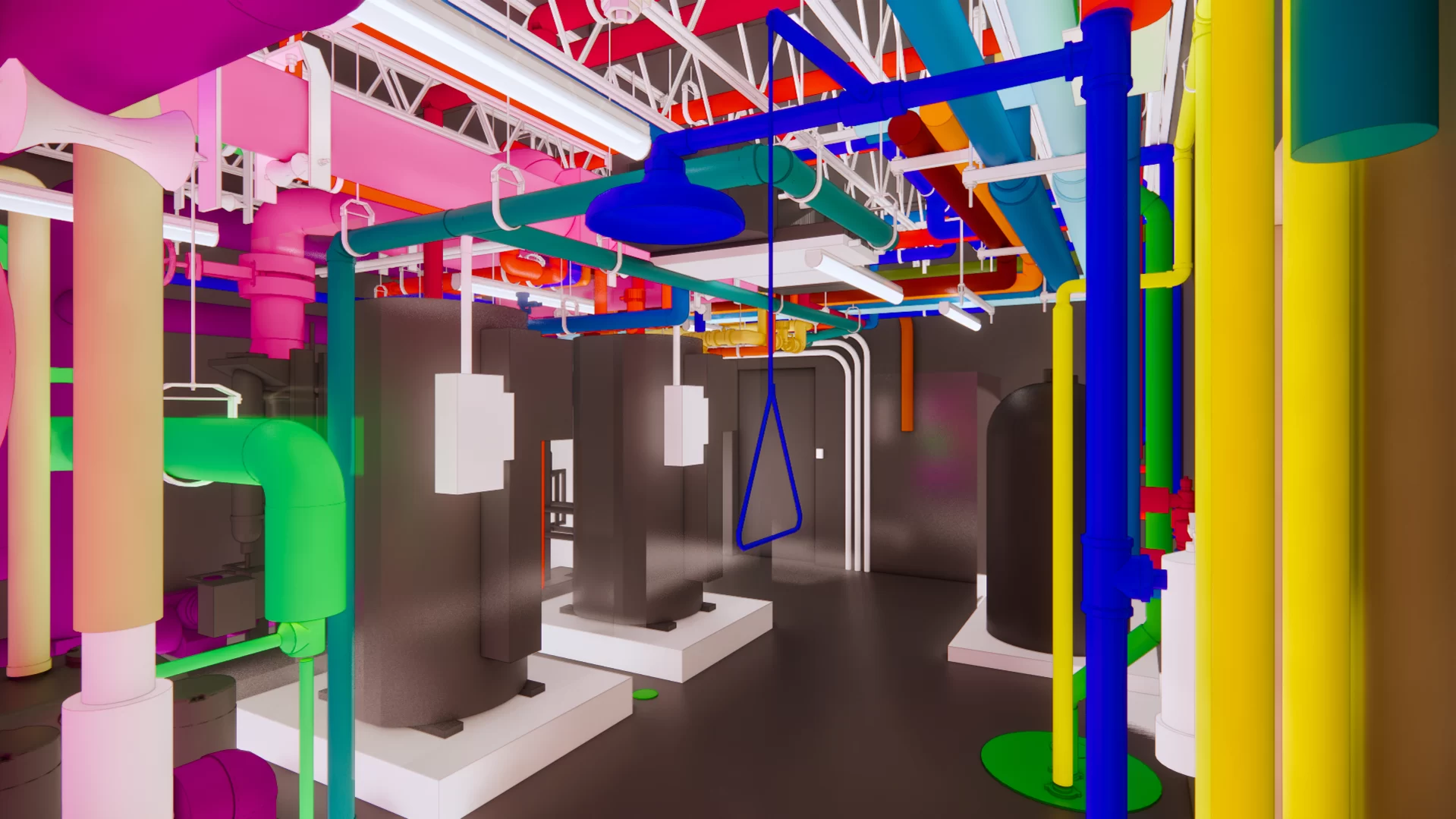
Such as? “It’s all that rough stuff,” says Bates project manager Chris Streifel — “rough” in the sense of coarse. “There’s still some work to be done on leveling floors. There’s building [interior] walls, getting them ready and closing them in. There are structural things on the ceilings.”
“That’s how we’ll go for probably another month or so,” by which point it should be easier to get a sense of the future Dana as rooms are partitioned into their final configurations. “There’s a lot of work to do, but it’ll come together pretty quick in a lot of spaces.
“It’s not imminent, but it’s not a year away.”
And of course there’s always the impressive drive to hang utilities apparatus from ceilings in all five levels of the building. (So, even with the air handler out of sight, an observer still has plenty of looking upward to do.) In fact, there are so many new pipes, conduits, air ducts, etc., destined to crisscross the ceilings that we asked Streifel whether the renovation would leave Dana with substantially more such infrastructure after the renovation than before it.
The answer is an empirical and qualified “yes.” Post renovation, there “probably is a little bit more, just because building systems are more complicated” than they used to be, Streifel says.
In addition, a major gain is coming with the new HVAC system, which addresses longtime shortcomings in the previous setup. Back in the day, Dana was infamous for its spotty temperature regulation, which was addressed but never quite remedied by upgrades to the original 1965 air handling machinery and the addition of several supplementary systems, some of them serving single labs.
But after the makeover, thanks to the creation of a single, state-of-the-art system, Dana occupants will enjoy “heating and cooling throughout the building consistently, as opposed to pockets of cooling [or warming] here and there,” Streifel says.
And in addition to the new attic HVAC machine, the latest system will comprise masses of ductwork, water and steam pipes, and overhead fan-coil units that provide zonal temperature control. A tour of the building reveals heaps of such equipment, intakes sealed against dust with attractive blue plastic, awaiting installation.
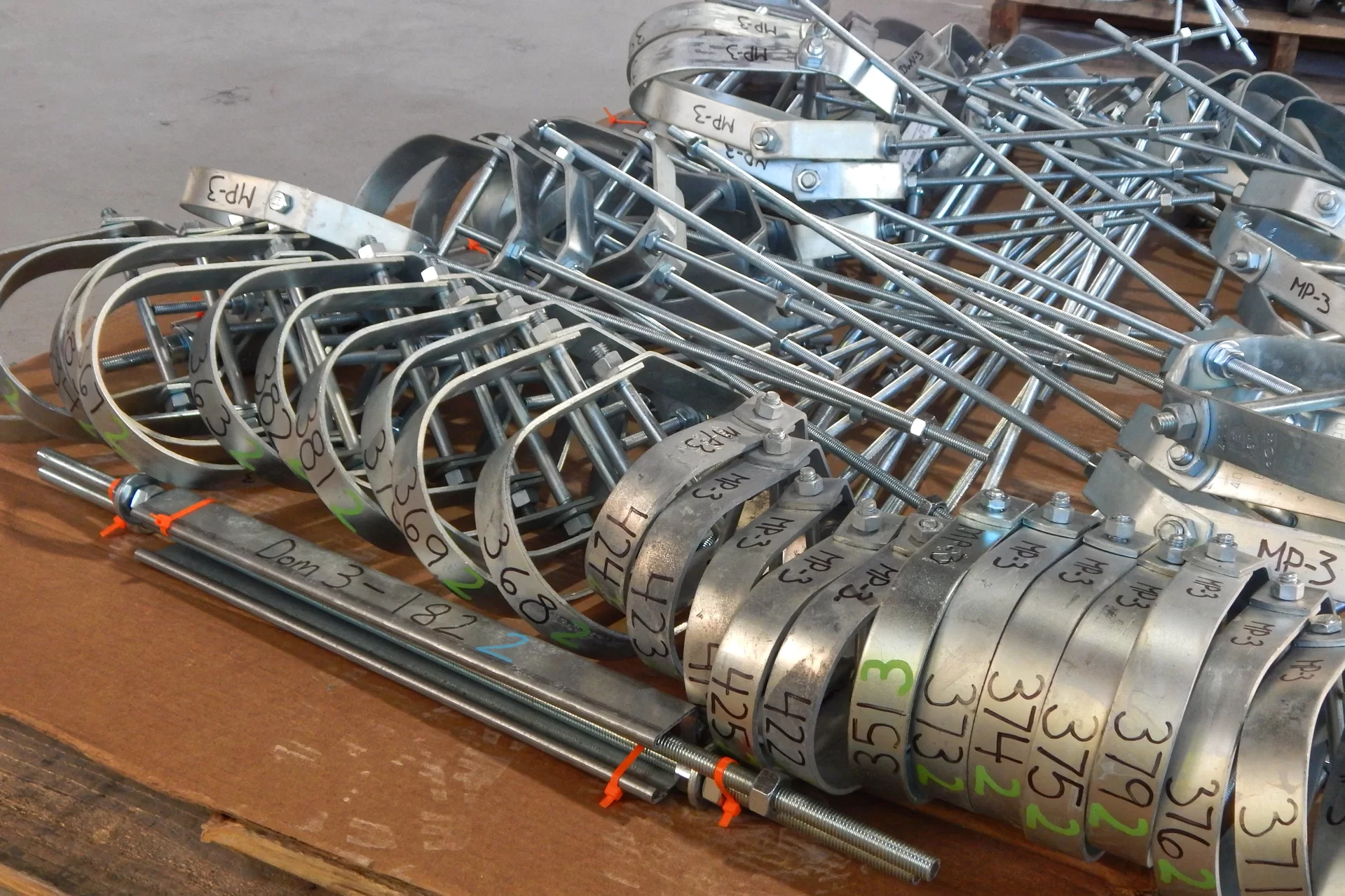
Reductions in other utilities, though, will somewhat offset all that new overhead HVAC metal. This is driven by a change in the building’s mission: Because research that had taken place in Dana has been moved to the new Bonney Science Center and Dana’s new labs will be oriented more toward introductory instruction (in biology and chemistry), they won’t require the previous density of domestic water supplies, drainage, etc., that was present before.
Having addressed a defining question of these troubled times — which version of Dana, past or future, has more pipes hanging from the ceilings? — we can now move on to another overhead process, begun in December, that may be a bit more consequential. Steelworkers for the local subcontractor MZ Metal Works are nearly finished installing short girders that on one end are fastened to Dana’s structural steel skeleton, and at the other are bolted into the building’s masonry exterior walls.
Manufactured by American Steel Fabricators of Greenfield, N.H., and sometimes called “clips,” these units improve “the seismic resistance of the building,” Streifel explains — that is, their stability during an earthquake. They impart additional rigidity to the structure and “help keep things in place and straight so they’re providing their maximum load capacity.”
Another ceiling operation that’s just about done is the spraying-on of a material called K13. This provides both sound absorption and a kind of industrial-chic visual effect that makes an open ceiling look pretty good, despite all the pipes and wires (and eventually, laced-together pairs of sneakers) dangling up there. It’s one of the elements used by architectural firm Payette, designer of both the Dana renovation and the new Bonney Center, to provide visual unity between the two buildings.
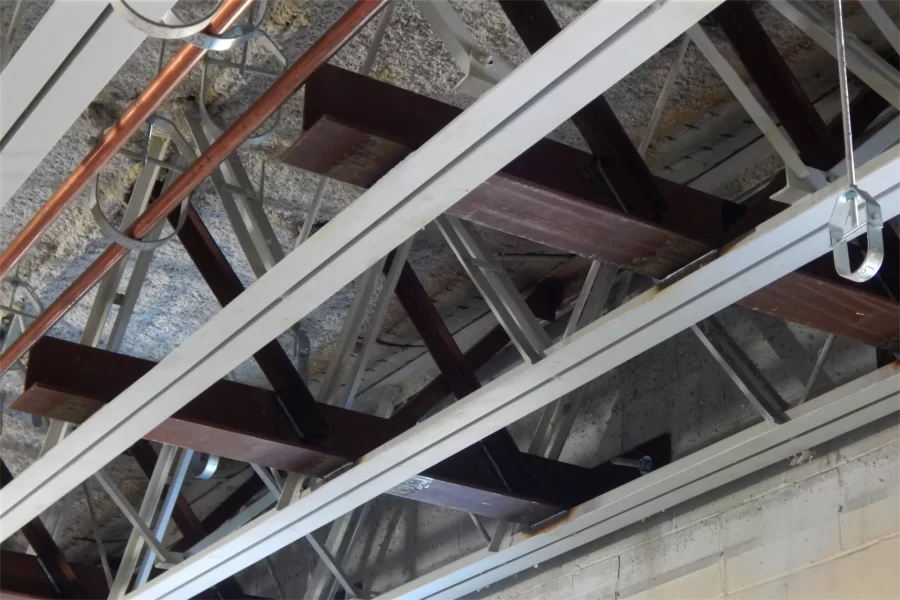
No delays in virus delivery: Speaking of defining questions of these troubled times — but seriously now — we wondered how the pandemic is affecting workers and the pace of work at Dana. It’s certainly making some workers ill or otherwise keeping them off the job, says Streifel, but the project remains on schedule — thus far. “It’s adding strain. We haven’t gotten to the point where we’ve had to make any adjustments, but it’s a real possibility that we’re monitoring.”
As was the case during Bonney Science Center construction, project management firm Consigli Construction is responsible for safety protocols on the Dana site.
And what about snarls in the supply chain? With construction likely to be complete by early summer, “there are still plenty of opportunities for things to go sideways,” Streifel replies, “but so far, so good.” He adds, “a lot of that has been managed by just being more proactive, ordering things much earlier, answering questions much earlier.”
In fact, the timely Nov. 29 delivery of that giant complex air-handling unit was a Dana success story in the global realm of supply-chain woes. “That’s no small deal,” he says, pointing to the way the semiconductor shortage has gummed up automakers. “That’s where a lot of the long lead times have really started — things that have so many different components, so a lot of different opportunities” for things to go off the rails. (So far, by the way, we haven’t heard about any shortages of chains linked to global supply chain issues. Or maybe, as Gerry Goffin wrote and The Cookies sang, they ain’t the kind that you can see.)
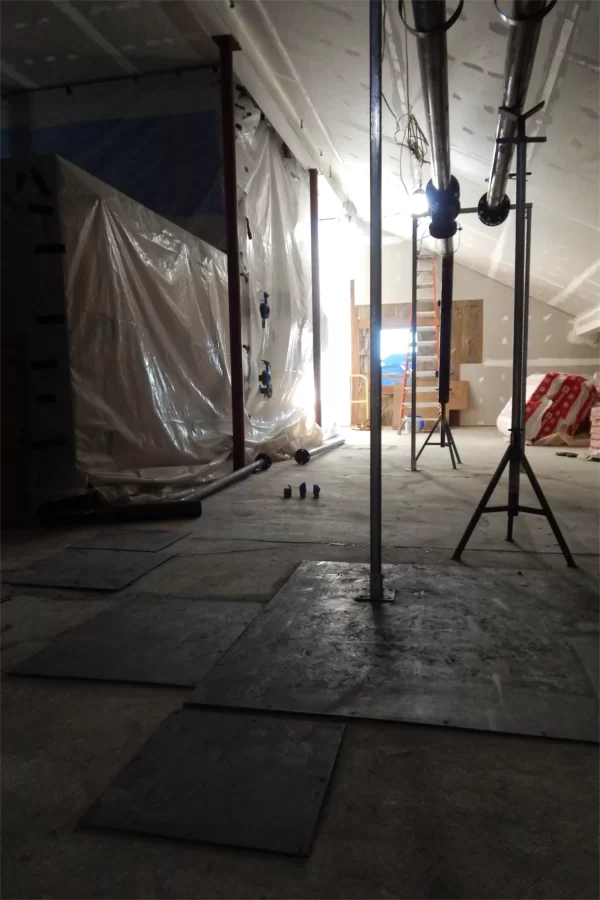
Anyhoo, back to the topic of progress. If the crane acrobatics gave that HVAC unit a certain charisma it will never have again (except perhaps in the fond eyes of Campus Construction Update), its delivery and activation, more importantly, will make possible all kinds of progress in the mechanical, electrical, and plumbing installations, and by extension, on most fronts throughout the Dana renovation.
“It allows us to bring all the big ductwork up there, to start wiring up all the power — I think there are nine electrical circuits that connect to the various aspects of that machine,” says Streifel. “And I don’t know how many different pipes in and out.
“All of that can happen because now they have set points” on the air handler that they can connect to. “They could have run them close by before that, and just waited for the machine to be there, but this makes it that much easier.”
Can we talk? Campus Construction Update loves to hear from you. Please send your questions, comments, and reminiscences about construction at Bates College to dhubley@bates.edu, with “Campus Construction” or “A lot of what you write about is really over your head, isn’t it?” in the subject line.
