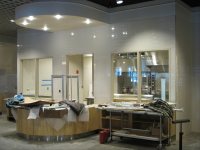
Greening the grid: That’s how Bates characterizes its latest initiative in the effort to stay sustainable.
The college is partnering with ReVision Energy, a leading solar facilities provider in Maine, to establish a photovoltaic array on more than 20 acres of countryside in the town of Skowhegan. The array will comprise nearly 18,500 panels and feed into the regional grid 7.131 megawatts of direct current, or DC, which will be converted to alternating current, or AC, for grid distribution to businesses and residences.
That’s about three-quarters of the college’s electrical usage, says Tom Twist, Bates’ sustainability manager. The array itself will be the largest ReVision has built to date, although it’s working on others of comparable size.
The project is scheduled to begin generation this summer, barring a recurrence of supply chain issues that have affected electrical components in particular.
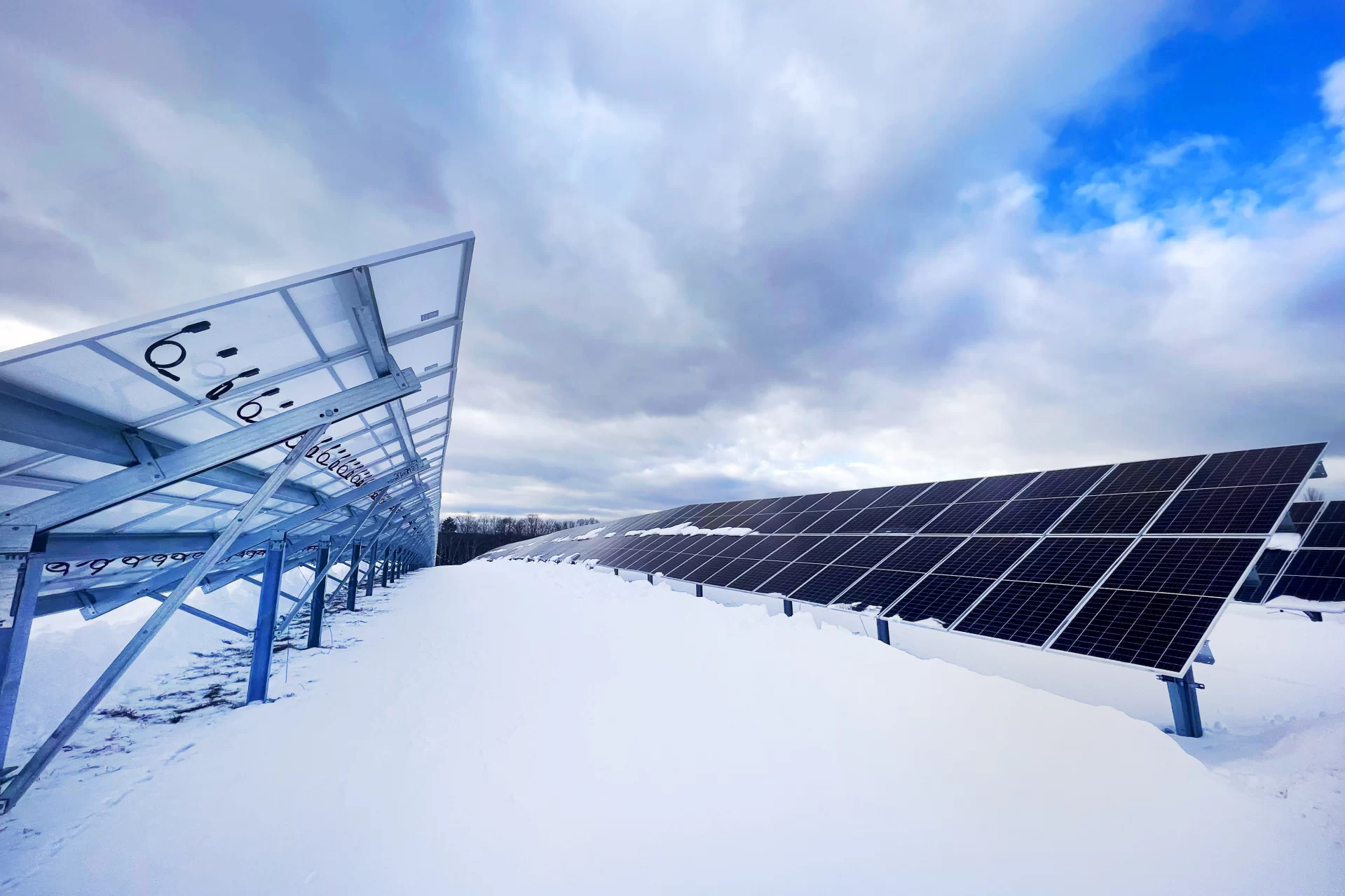
To be clear, Bates has met its electrical needs with renewable power since 2005, when the college began sourcing its juice in the form of Renewable Energy Certificates, or RECs, from Maryland-based Constellation Energy. In effect, RECs are documents affirming that a certain amount of power has been generated sustainably. (The college will continue to buy RECs for the roughly 25 percent of its electrical usage not produced by the solar array.)
What the Skowhegan project will change, though, is that Bates, in partnership with ReVision, will take direct responsibility for creating its own green electricity.
Leased for the solar project by landowner Jim Henshaw, a farmer, the construction site is open land some distance back from Eaton Mountain Road.
“It’s kind of hidden and tucked away in there, surrounded by forest,” says Brian Byrne, the ReVision project manager overseeing the construction. (The staff land developer for ReVision who helped put the lease arrangement together is Holly Noyes ’10, who is also a farmer.)
In some ways, the site was a solar installer’s dream. “It’s a nice, beautiful, wide-open field. We didn’t have to clear any trees,” Byrne explains. It’s heavily vegetated and very well-drained, meaning that there are no wetlands, no areas vulnerable to erosion, and no threat of stormwater runoff or sediment washing off the site. “From a Department of Environmental Protection perspective, this has been the greatest site we’ve ever dealt with.”
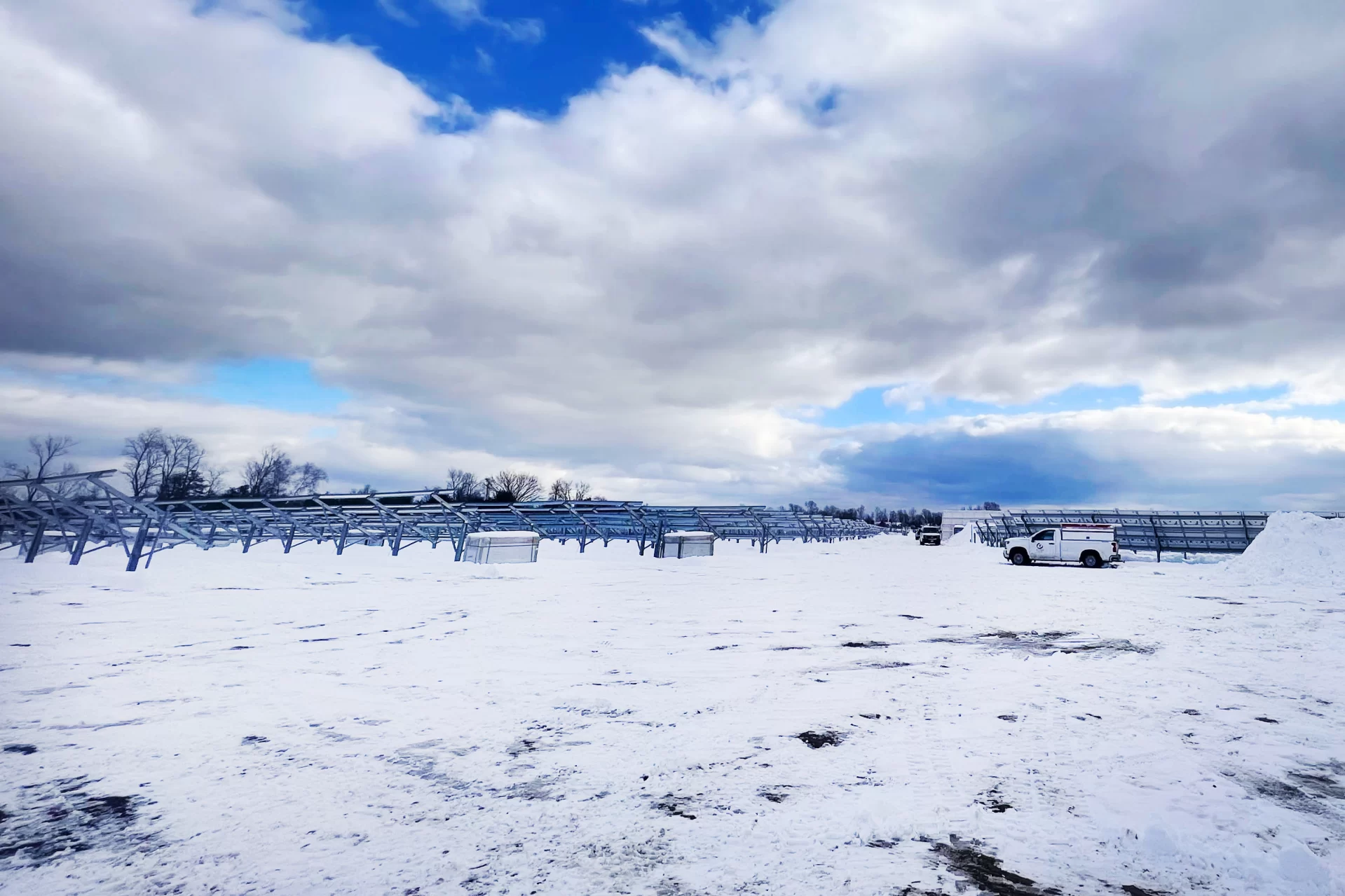
Sullying the dream, though, were conditions three or four feet below the soil surface. Typical for a ground-level PV array, the Bates project consists of long rows of solar panels, aka modules, attached to “racks” — horizontal rails mounted on steel piles that are driven into the earth. So pile driving was the first order of business when construction began last summer. And cue the tension-building music:
“We thought this was just going to be a very deep soil, like a sandy loam,” says Byrne, “but it’s actually incredibly compact, dense clay when you hit about three feet” below the surface, punctuated with boulders. (Marine clay strikes again!)
As is its wont, the clay all but stalled progress. “This site appeared to be a dream from the surface,” says Byrne, “but once we started driving these steel piles, which support the racking, we could not drive them in.” Between the clay and the underground boulders, fully half of the 2,500 piles couldn’t be driven to the depth necessary — below the frost line, more than six feet under.
“To make matters worse, we could not pull them back out because it was such compacted clay. The amount of force [necessary] was unbelievable. It just seemed to defy physics,” Byrne says. “So we had to dig them out.”
In the end, Gardiner-based Maine Drilling & Blasting came in to pre-drill holes for the undrivable half of the piles, which are 16-foot steel I-beams.
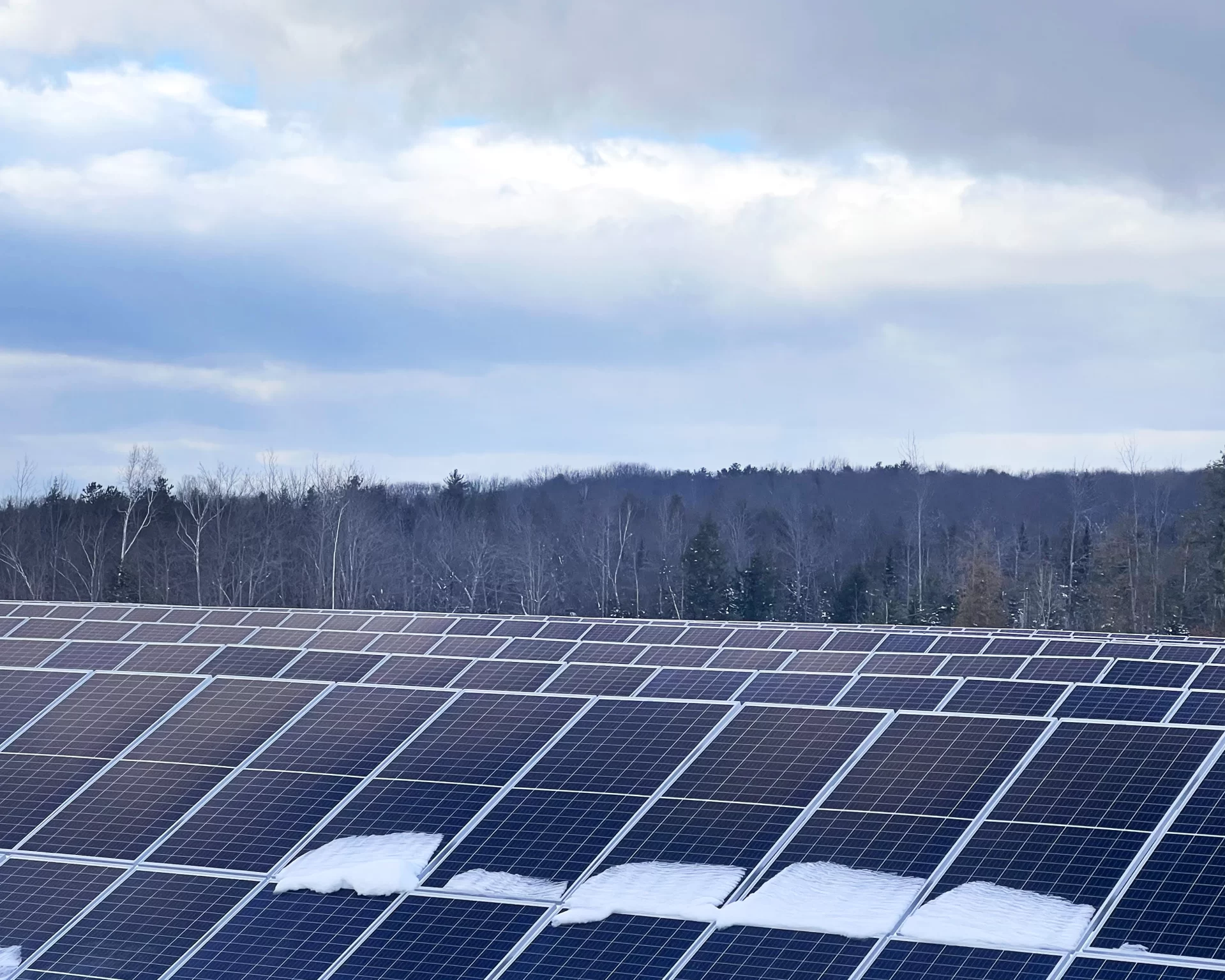
“In our ideal world, we wanted all of the modules to be mounted to the racking by the end of December, and that did not happen because the racking was so delayed.”
For the sake of context, the company fabricating and placing the racks, RBI Solar of Cincinnati, “was anticipating 12 to 14 weeks to complete this project.” Now completing final punch list items, “they’re on week 26.”
“This was the greatest delay we’ve ever encountered for installing racking,” Byrne says.
Which is not to say that the trials of the piles stalled the project outright. “If there’s an obstacle, we move around it and keep pushing forward,” says Byrne. “While we were delayed with racking, there were other things to do.” In conjunction with a regular business partner, Gifford Electric of Brewer, Maine, the project team installed utility poles, equipment racks, DC combiners and transformers; dug trenches for electric lines; and pulled conduits.
As this was written, about 60 percent of the 18,486 modules were in place. Two types of solar modules, one slightly more powerful than the other, are being used. Rated at 395 watts is a model made by the German company Qcells: 7,098 of those will be installed. REC Solar produces the other module: 11,388 of those at the Bates site will each generate 380 watts.
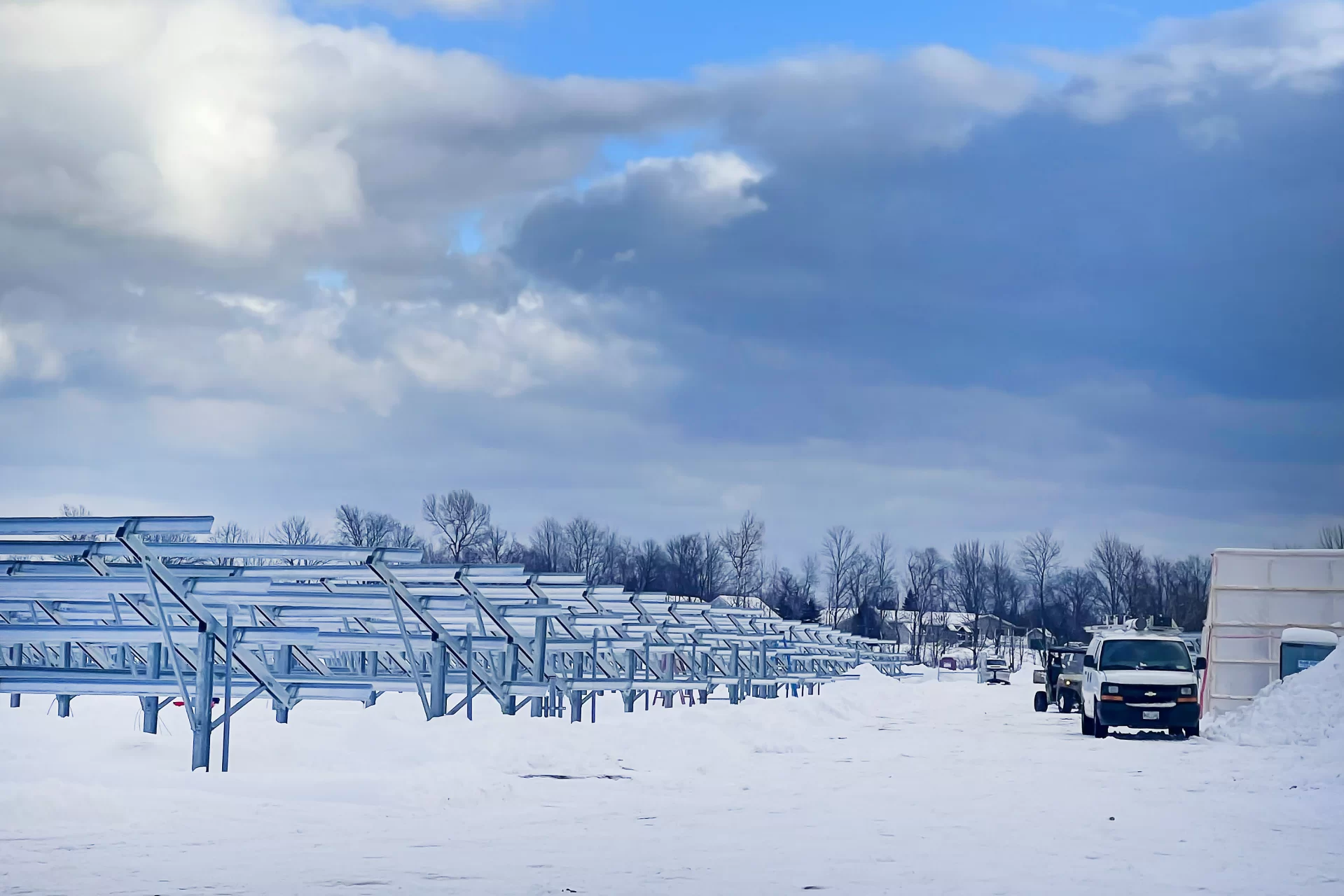
(In short, here’s more about AC/DC, and we’re not discussing Angus Young’s stage attire: Sunlight on solar panels generates DC, which is converted to AC for long-distance distribution. The Skowhegan solar plant will inject about 5 MW of AC current into the grid.)
Each type weighs just over 50 pounds apiece and measures about 80 by 40 inches. Byrne explains that installation is a succession of steps performed in waves by just a handful of people — pre-positioning components, attaching some hardware, placing the lower row of modules, attaching more hardware, placing the upper row of modules.
On average, in benign conditions, a useful rule of thumb is that during a nine-hour day, one installer can mount approximately 75 lower-rack modules or 50 on the upper section.
“Everything is prepared before the crew does the task, and that’s how we can maintain efficiency. It stays very organized, very clean. There’s no garbage blowing around the field.” In fact, Byrne adds, “Solar is my favorite construction project. It’s not a typical construction site. Once the excavation’s done and you pound the posts, these are the only silent construction sites there are, and it’s fantastic.
“If you can hear the birds, and watch the leaves blow and the grass bend, that’s pretty ideal.”
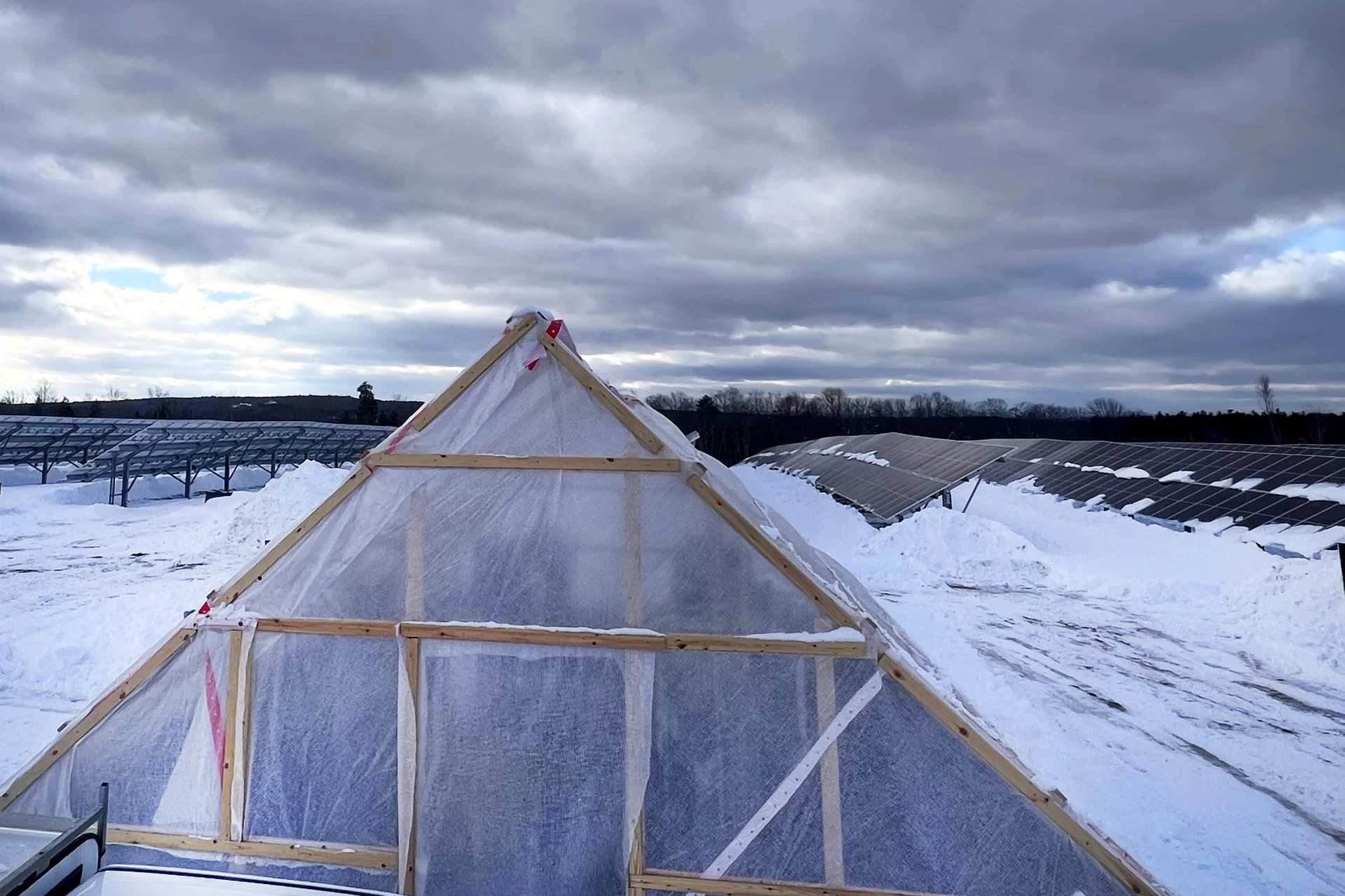
Not to mention listening to the munching of sheep on the grass that will continue to grow at the project site. Historically used for hay cutting and on-site grazing, Henshaw’s land will continue to support haying twice a year, as prescribed by a land-use permit, and grazing any old time.
Bates and ReVision have worked together for years, one high-profile result being the installation, over two years, of rooftop solar at the Bates Coastal Center at Shortridge.
The current (no pun intended, but it’s not bad) collaboration dates to the years just prior to the pandemic. Driven in part by strong student interest in sourcing Bates electricity from large-scale solar, the college undertook a rigorous exploration of its options.
In 2019, the state of Maine enacted legislation that in various ways advanced the cause of renewable energy. One of those bills, L.D. 1711, made financial outcomes “much more fair for large solar electricity customers,” explains Tom Twist, Bates’ sustainability manager.
“As soon as that was passed, we were able to hit the ground running” in developing a workable model for involvement in a solar farm. That contrasts with a number of other large solar projects in Maine that are still hanging fire, Twist says. “We feel really lucky that this is going through.”
As a member of the Bates EcoReps, students who undertake a variety of campus sustainability projects, economics major Kyung Phil “KP” Ko ’22 was one of several involved with that modeling process. “We dug into the proposals sent over by a few parties, ReVision being one of them, to really understand what the benefits to Bates would be,” explains Ko, who now analyzes U.S. utilities and power issues for Scotiabank.
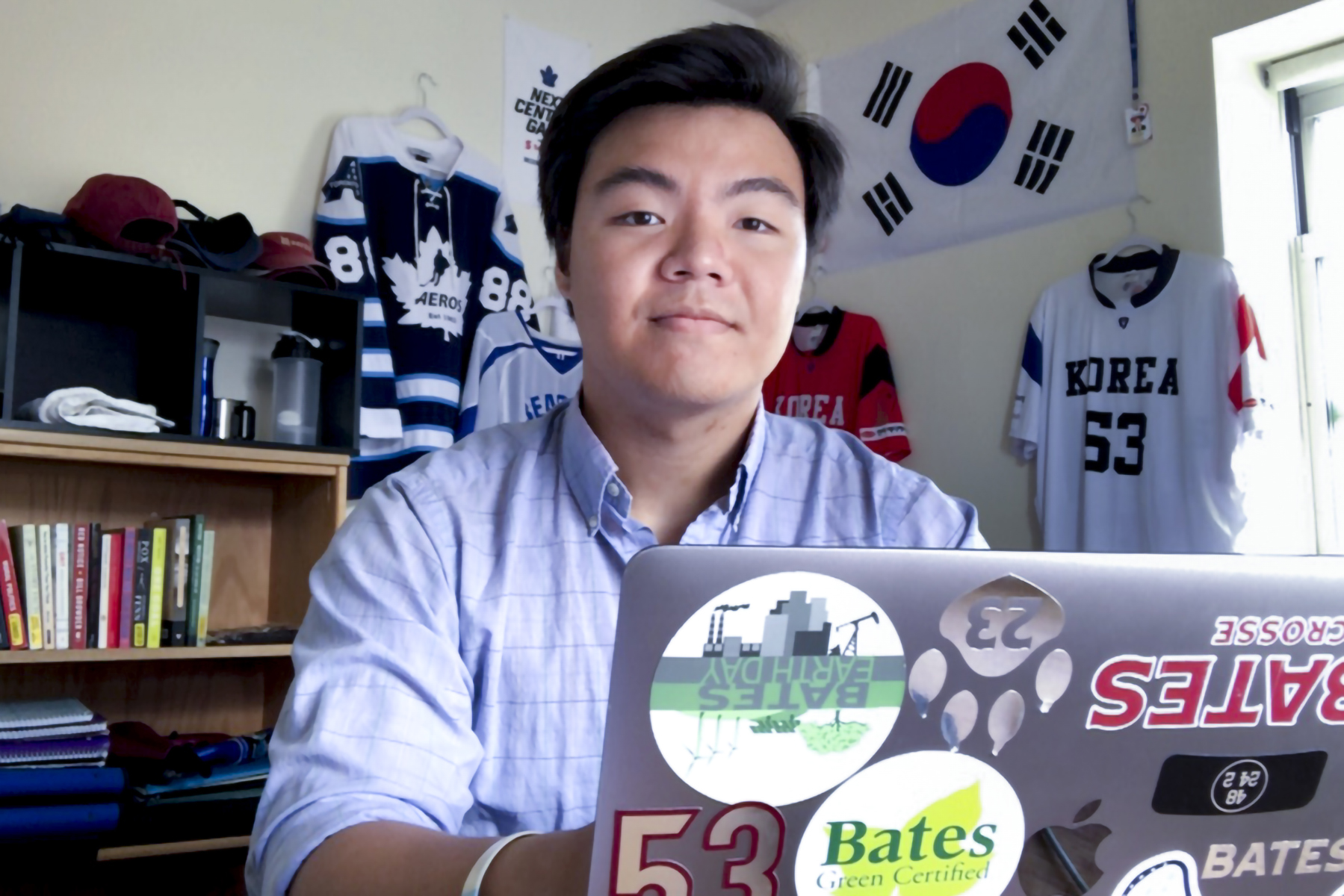
“Once the benefits were understood, we worked this up the decision-maker chain. To be exact, the arrangement was a financial PPA, where Bates could hedge against the volatility of electricity bills thereby bringing us cost savings and monetizable renewable energy credits.”
“Reaching construction is a humongous milestone worthy of hoots and holler.”
KP Ko ’22
“I can’t tell you how happy I am that the project has reached the construction stage,” Ko adds. “Working in the renewable energy investment banking space, I can tell you that the industry has faced incredible uphill battles over the past year with supply chain issues, inflation, bloated interconnection queues, and what almost was the end of solar investment tax credits.
“Reaching construction is a humongous milestone worthy of hoots and holler. I hope to visit Maine sometime soon and see the arrays for myself.”
The work of Ko, his classmate Tamsin Stringer, and other students was invaluable to the project. “To figure out the costs, figure out the net value of solar electricity several years into the future — all those things were complicated, and the students did a really nice job,” says Twist. “Really professional-level.”
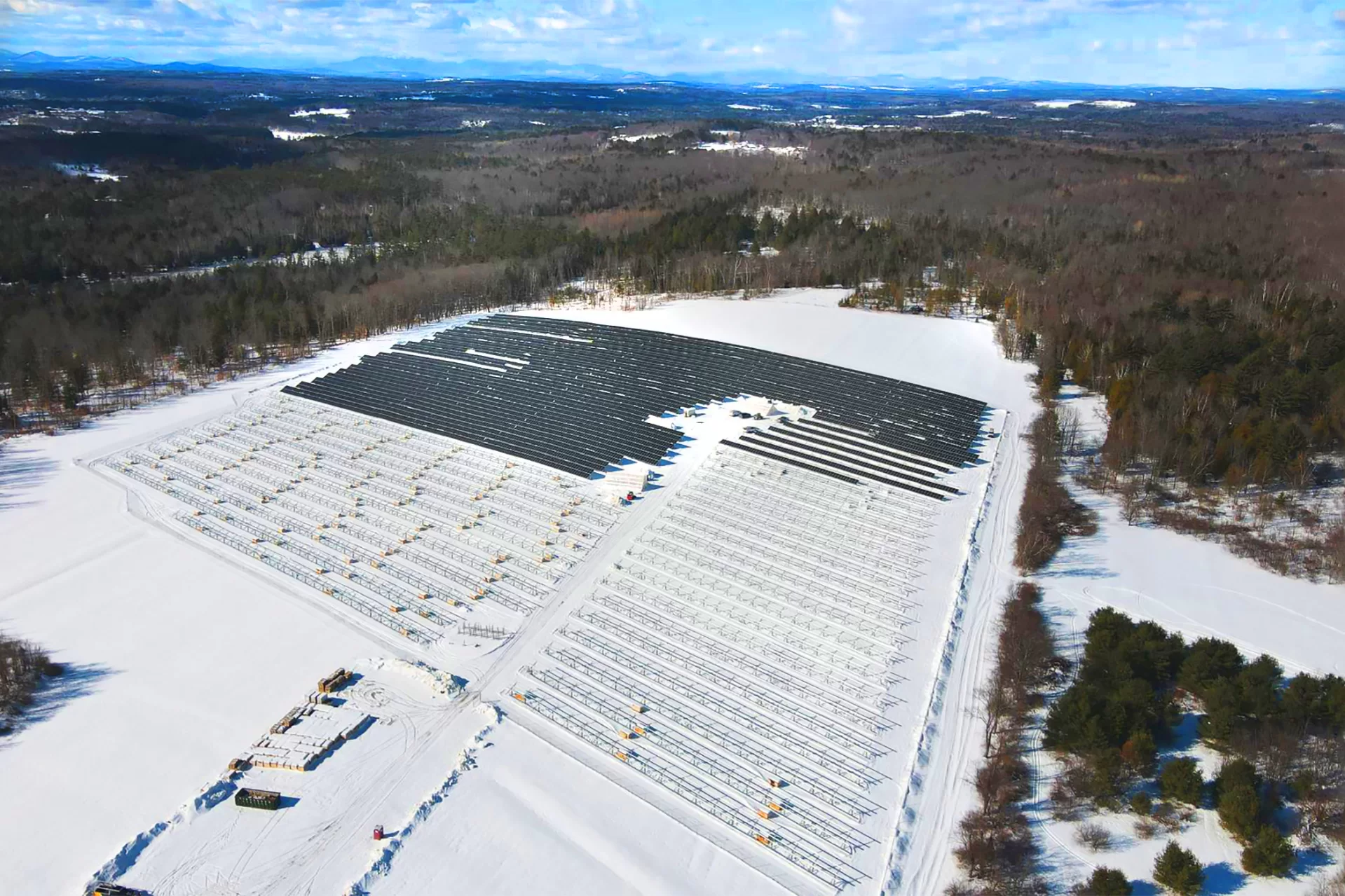
He adds, ReVision “knows the ins and outs of the solar market around Maine, and they were really able to help us. I think if we went with someone who wasn’t familiar with Maine, we’d still be stuck.”
In sum, when Bates saw the opportunity to go solar in a big way, “we were ready for it,” says Geoff Swift, the college’s vice president for finance and administration and treasurer. “There were things that had to happen before other things could happen, so it took a long time to get to where we are today.
“But it’s thrilling to have the array in process and going up in Skowhegan.”
Can we talk? Campus Construction Update wants to hear from you. Please send your comments and questions about construction at Bates, as well as your feelings about marine clay, to dhubley@bates.edu, with “Campus Construction” or “What do sheep count when they can’t sleep?” in the subject line.